Bronze
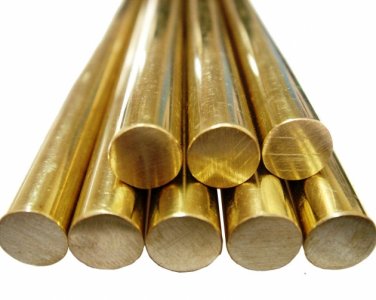
Bronze is an alloy based on copper and tin, where the alloying components can be beryllium, aluminum and other elements, most often phosphorus, aluminum, zinc and lead. But still bronze cannot be an alloy of copper with zinc (then you get brass) or alloys of copper with and nickel.
Relevance
The most famous bronze tin is an alloy of copper and tin (coppermostof the time). This is one of the first metals mastered by man. People have known this composition since the ancient Bronze Age. For a long time bronze was a strategic metal (up to XIX century cannons were cast from bronze). This metal is remarkable for its qualities such as hardness, durability and high manufacturability. The discovery of bronze opened up great prospects for man. To view prices of nonferrous metals and to buy bronze you can visit our site.
Properties
Tin bronze is poorly machined by pressure, poorly cut and bent. It is a foundry metal and its foundry qualities are not inferior to other metals. It is characterized by low shrinkage — 1−2%, shrinkage of brass and cast iron = 1.6%, steel — more than 3%. That is why bronze is successfully used for complex artistic castings. It has high corrosion resistance and antifriction properties. It is used in chemical industry for making fittings and as antifriction material for moving units.
Bronze grades
Tin bronzes can be further alloyed with zinc, aluminum, nickel, phosphorus, lead, arsenic and other metals. Addition of zinc (not more than 11%) does not change the bronze’s characteristics, but makes it much cheaper.
Alloy | Fe | Ni | As | Cu | Pb | Zn | Р | Sn | Impurities |
---|---|---|---|---|---|---|---|---|---|
BROF2−0.25 | ≤0.05 | ≤0,2 | --- | 96,7−98,98 | ≤0,3 | ≤0.3 | 0,02−0,3 | 1−2,5 | ≤0,3 |
Bronze with zinc addition is called «Admiralty Bronze» and is very resistant to corrosion in sea water. Lead and phosphorus improve anti-friction properties of bronze. Aluminum bronze is lightweight and high specific strength.
Si | Fe | Mn | Al | Cu | Pb | Zn | Р | Sn | Impurities |
---|---|---|---|---|---|---|---|---|---|
≤0.1 | 2−4 | 1−2 | 9−11 | 82,3−88 | ≤0,03 | ≤0.5 | ≤0.01 | ≤0.1 | ≤0,7 |
It is in demand in transport engineering. Its high electrical conductivity is important in electrical engineering. Beryllium bronze parts do not spark on impact and are used in explosive environments.
Alloy | Fe | Si | Al | Cu | Pb | Zn | Be | Ni | Impurities |
---|---|---|---|---|---|---|---|---|---|
BrB2 | ≤0.15 | ≤0,15 | ≤0,15 | 96,9−98 | ≤0,005 | --- | 1,8−2,1 | 0,2−0,5 | ≤0,6 |
A number of copper alloys are not bronzes. The best known of them are brass (Cu+Zn alloy) and constantan (Cu+Ni).
Supply
We supply certified nonferrous rolled steel and bronze alloys at the best prices. The specification reflects the data on the percentage composition and mechanical properties of products. From us it is easy to buy in bulk any semi-finished products for large-scale production. We provide favorable conditions for retail buyers. Our company has a high level of service and responsiveness of service.
Buy at a bargain price
All production from rare and nonferrous metals sold by Evek GmbH meets GOST and international quality standards. You can buy bronze in the shortest possible time. High quality, reasonable prices and a wide range of products determine the face of our company. Becoming our regular customer you can count on a system of discount discounts. Cooperation with us will help you realize any engineering plans. We are waiting for your orders on our site.
Bronzes
Bronzes are copper-based alloys containing more than 2.5% (by mass) of alloying components.
In bronzes the zinc content should not exceed the content of the sum of other alloying elements, otherwise the alloy will be referred to as brass.
Bronzes are named by the main alloying element (aluminum, tin, etc.), although in some cases by two or three (tin-phosphoric, tin-zinc, tin-zinc-lead, etc.).
Tin-free bronzes
The summary list of Russian standard pressure-treated tin-free bronzes and their foreign analogous alloys is given in Table 1.
The summary list of domestic standard pressure-treated sulfide-free bronzes and their foreign analogues alloys
Low-alloy bronzes:
Bronze grade | US analogue | Analog German | Japan | Note |
---|---|---|---|---|
BrSr0,1 | - | CuAg0.1 (2.1203) | - | silver (Ag) |
- | - | CuAg0.1P (2.1191) | - | silver (Ag) |
Tellurium bronze | С14500 | CuTeP (2.1546) | - | tellurium (Te) |
- | C19600 | - | - | ferrous (Fe) |
- | C19200 | - | - | ferrous (Fe) |
- | C19500 | - | - | ferrous (Fe) |
- | C19400 | CuFe2P (2.1310) | - | ferrous (Fe) |
- | - | - | C1401 | others |
BrMg0,3 | - | CuMg0.4 (2.1322) | - | others |
- | C14200 | - | - | others |
- | C14700 | CuSP (2.1498) | - | miscellaneous |
- | - | CuZn0.5 (2.0205) | - | others |
- | - | CuMg0.4 (2.1322) | - | others |
- | - | CuMg0.7 (2.1323) | - | others |
- | C15100 | CuZr (2.1580) | - | others — |
BrX1 | - | - | - | others |
- | C18400 | CuCrZr (2.1293) | - | others — |
BrKd1 | - | - | - | others |
- | - | CuPbIp (2.1160) | - | others |
Aluminum bronzes:
Bronze grade | US analogue | Same as Germany | Same as Japan | Note |
---|---|---|---|---|
BrA5 | C60800 | CuA15As (2.0918) | - | Al-Cu |
BrA7 | - | CuA18 (2.0920) | - | Al-Cu |
- | C61400 | CuAl8Fe3 (2.0932) | C6140 | Al-Fe-Cu |
- | C61300 | - | - | Al-Fe-Cu |
BrAJ9−4 | C62300 | - | - | Al-Fe-Cu |
Same | C61900 | - | - | Al-Fe-Cu |
- | C62400 | - | - | Al-Fe-Cu |
БрАМц9−2 | - | CuA19Mn2 (2.0960) | - | Al-Mn-Cu |
БрАМц10−2 | - | - | - | Al-Mn-Cu |
- | С64200 | - | - | Al-Si-Cu |
- | С64210 | - | - | Al-Si-Cu |
BrAJMc10−3-1b5 | - | CuA10Fe3Mn2 (2.0936) | - | Al-Fe-Mn-Cu |
БрАЖН10−4-4 | C63000 | CuA110Ni5Fe4 (2.0966) | - | Al-Fe-Ni-Cu |
- | - | CuA111Ni6Fe5 (2.0978) | - | Al-Fe-Ni-Cu |
- | - | CuA19Ni3Fe2 (2.0971) | - | Al-Fe-Mn-Ni-Cu |
- | - | - | C6161 | Al-Fe-Mn-Ni-Cu |
- | - | - | C6280 | Al-Fe-Mn-Ni-Cu |
BrAJNMc9−4-4−1 | C63200 | - | C6301 | Al-Fe-Mn-Ni-Cu |
- | C63800 | - | - | Al-Si-Co-Cu and Al-Si-Ni-Cu |
- | C64400 | - | - | Al-Si-Co-Cu and Al-Si-Ni-Cu |
Beryllium bronzes:
Bronze grade | US analogue | Same as Germany | Japan |
---|---|---|---|
- | C17410 | - | - |
- | C17510 | CuNi2Be (2.0850) | - |
- | C17500 | CuCo2Be (2.1285) | - |
- | C17000 | CuBe1.7 (2.1245) | C1700 |
БрБ2 | C17200 | CuBe2 (2.1447) | C1720 |
- | - | CuBe2Pb (2.1248) | - |
BrBET1.9 | - | - | - |
BrBNT1,9Mg | - | - | - |
Siliceous bronzes
Bronze grade | US analogue | Same as Germany | Same as Japan |
---|---|---|---|
- | - | CuNi1.5Si (2.0853) | - |
- | C64700 | - | - |
BrKN1−1 | - | CuNi2Si (2.0855) | - |
- | - | CuNi3Si (2.0857) | - |
- | C70250 | - | - |
- | C65100 | - | - |
BrKMts3−1 | - | - | - |
Same | C65500 | - | - |
Manganese bronze
Bronze grade | US Analogue | Same as Germany | Japan Analogue |
---|---|---|---|
BrMz5 | - | - | - |
Tellurium bronze in GOST 18175 has no special designation
Table 2. Chemical composition of tin-free bronzes (GOST 18175−78) (mass fraction, %)
Mark | Content Limit of Elements | Cu | Ag | Al | Be | Cd | Cr | Fe | Mg | Mn | Ni | P | Pb | Si | Sn | Te | Ti | Zn | Sum of other elements |
---|---|---|---|---|---|---|---|---|---|---|---|---|---|---|---|---|---|---|---|
BrA5 | min. | ost. | - | 4,0 | - | - | - | - | - | - | - | - | - | - | - | - | - | - | - |
BrA5 | max. | - | - | 6,0 | - | - | - | 0,5 | - | 0,5 | - | 0,01 | 0,03 | 0,1 | 0,1 | - | - | 0,5 | 1,1 |
BrA7 | min. | ost. | - | 6,0 | - | - | - | - | - | - | - | - | - | - | - | - | - | - | - |
BrA7 | max. | - | - | 8,0 | - | - | - | 0,5 | - | 0,5 | - | 0,01 | 0,03 | 0,1 | 0,1 | - | - | 0,5 | 1,1 |
БрАМц9−2 | min. | ost. | - | 8,0 | - | - | - | _ | - | 1,5 | - | - | - | - | - | - | - | - | - |
БрАМц9−2 | max. | - | - | 10,0 | - | - | - | 0,5 | - | 2,5 | - | 0,01 | 0,03 | 0,1 | 0,1 | - | - | 1,0 | 1,5 |
БрАМц10−2 | min. | ost. | - | 9,0 | _ | - | - | _ | - | 1,5 | - | - | - | - | - | - | - | - | - |
БрАМц10−2 | max. | - | - | 11,0 | - | - | - | 0,5 | - | 2,5 | - | 0,01 | 0,03 | 0,1 | 0,1 | - | - | 1,0 | 1,7 |
BrAJ9−4 | min. | ost. | - | 8,0 | - | - | - | 2 | - | - | - | - | - | - | - | - | - | - | - |
БрАЖ9−4 | max. | - | 10,0 | - | - | - | 4 | - | 0,5 | - | 0,01 | 0,01 | 0,1 | 0,1 | - | - | 1 | 1,7 | |
БрАЖМц10−3-1,5 | min. | ost. | - | 9,0 | - | - | - | 2 | - | 1,0 | - | - | - | - | - | - | - | - | - |
БрАЖМц10−3-1,5 | max. | - | 11,0 | - | - | - | 4 | - | 2,0 | - | 0,01 | 0,03 | 0,1 | 0,1 | - | - | 0,5 | 0,7 | |
BrAJN10−4-4 | min. | ost. | - | 9,5 | - | - | - | 3,5 | - | - | 3,5 | - | - | - | - | - | - | - | - |
БрАЖН10−4-4 | max. | - | - | 11,0 | - | - | - | 5,5 | - | 0,3 | 5,5 | 0,01 | 0,02 | 0,1 | 0,1 | - | - | 0,3 | 0,6 |
БрАЖНМц9−4-4−1 | min. | ost. | - | 8,8 | - | - | - | 4 | - | 0,5 | 4,0 | - | - | - | - | - | - | - | - |
БрАЖНМц9−4-4−1 | max. | - | - | 11,0 | - | - | - | 5 | - | 1,2 | 5,0 | 0,01 | 0,02 | 0,1 | 0,1 | - | - | 0,5 | 0,7 |
BrB2 | min. | ost. | - | - | 1,8 | - | - | - | - | - | 0,2 | - | - | - | - | - | - | - | - |
BrB2 | max. | - | - | 0,2 | 2,1 | - | - | 0,15 | - | - | 0,5 | - | 0,05 | 0,15 | - | - | - | - | 0,5 |
BrBNT1.9 | min. | ost. | - | - | 1,85 | - | - | - | - | 0,2 | - | - | - | - | - | 0,10 | - | - | |
БрБНТ1,9 | max. | - | - | 0,2 | 2,1 | - | - | 0,15 | - | - | 0,4 | - | 0,05 | 0,15 | - | - | 0,25 | - | 0,5 |
BrBNT1.9Mg | min. | ost. | - | - | 1,85 | - | - | - | 0,07 | - | 0,2 | - | - | - | - | - | 0,10 | - | - |
BrBNT1,9Mg | max. | - | - | 0,2 | 2,1 | - | - | 0,15 | 0,13 | - | 0,4 | - | 0,05 | 0,15 | - | - | 0,25 | - | 0,5 |
Table 3. Characteristic properties and types of semi-finished products of tin-free bronzes
Bronze grade | Characteristic properties | Kinds of semi-finished products |
---|---|---|
БрАМц9−2 | High resistance under alternating loads | Bars, strips, bars, wires, forgings |
БрАЖ9−4 | High mechanical properties, good sliding properties, corrosion resistant | bars, tubes, forgings |
BrAJMc10−3-1.5 | Bad deformability in cold condition, deformable in hot condition, high strength at elevated temperatures, corrosion-resistant, high erosion and cavitation resistance | rods, pipes, wires, forgings |
БрАЖН10−4-4 | Badly deformed in cold state, deformed in hot state, high strength at elevated temperatures, corrosion-resistant, high erosion and cavitation resistance | bars, tubes, forgings |
БрБ2, БрБНТ1,9 | High strength and wear resistance, high spring properties, good sliding properties, medium electrical and thermal conductivity, very good deformability in quenched state. | Bands, strips, bars, tubes, wires. |
BrKMts3−1 | highly corrosion-resistant, weldable, heat-resistant, high compressive strength | Sheets, strips, bands, rods, wires |
BrKN1−3 | High mechanical and technological properties, corrosion resistant, good antifriction properties | Sheets, strips, strips, bars, wires |
Fig. 1. Diagram of system state (equilibrium state)
The diagram shows that the maximum solubility of aluminum in copper in the solid state is 9.4% (by mass). With increasing temperature from 565 to 1037 °C the solubility of aluminum in copper decreases and reaches 7.5%.
The stable phases of the Cu-Al system include α, β, γ2 and α2 phases.
The α phase is the primary solid solution, isomorphic, with an elementary face-centered cubic crystal lattice. When the alloy is slowly cooled to 400 °C, the α-phase forms a near-order, which leads to a marked decrease in its electrical resistivity, which continues even at temperatures below 200 °C as a result of the elimination of packing defects.
The β-phase is a solid solution formed based on the stoichiometric composition of Cu3Al directly from the melt at 1036−1079 °C, with an elementary centered cubic crystal lattice. The β -phase is ductile, electrically conductive and stable at temperatures above 565 °C. When the alloy is cooled rapidly (at a rate >2°C/min), it undergoes sharp martensite-type transformations, forming intermediate phases (Fig. 1). During slow cooling (2°C/min) β -phase disintegrates into eutectoid α+γ2 forming coarse-grained γ2 phase, which is released in the form of continuous chains, giving the alloy brittleness. Phase γ2 (Cu9Al4), formed from phase γ', is stable at low temperatures, brittle and hard, with electrical conductivity lower than that of β-phase.
Phase α2, formed at 363 °C as a result of peritectoidal reaction between phases α and γ2, has a face-centered cubic crystal lattice, but with different parameters.
Metastable phases in alloys: β1 — with elementary centered cubic crystal lattice (a — 5.84 Å, Al — 11.9%), ordered; β' — with elementary face-centered cubic crystal lattice (Al — 11.6%), very deformed; β1' — with elementary rhombic crystal lattice (a = 3.67 Å, c = 7.53 Å, Al — 11.8%), ordered; γ1-phase with an elementary orthorhombic cell (a = 4.51 Å, c = 5.2 Å, c = 4.22 Å, Al — 13.6%), ordered. It is assumed the existence of other phases, which are a kind of phase β1'.
Determining the structure of Cu-Al alloys is difficult. Very high cooling rates (from 1 to 8°C/min, depending on aluminum content) are required to obtain equilibrium alloy structures. Such structures are revealed by etching the alloys with ferric chloride.
However, ferric chloride etching does not always allow the phases in alloys cooled at the normal rate to be determined with certainty. In this case, special techniques using electrolytic polishing are used to reveal the true structure of Cu-Al alloys.
The structure of dual copper-aluminum alloys and multicomponent bronzes based on the copper-aluminum system in the equilibrium state is determined by the state diagram (Fig. 2).
Fig. 2. Diagram of phase transformations of aluminum bronze with aluminum content of 12.07% (by mass)
However, under production conditions in casting ingots and billets and their pressure treatment in hot and cold states, the rates of cooling and heating differ significantly from those at which the equilibrium diagram of state is constructed.
Therefore, the structures of cast and deformed semi-finished products also differ from those determined by the equilibrium state diagram.
To determine the properties and microstructure of alloys in the metastable state, C-curves are plotted showing the kinetics of phase transformation as a function of cooling rate and isothermal holding at temperatures below the eutectoid transformation temperature.
Single-phase alloys (α-aluminum bronzes) are ductile and well processed by pressure, two-phase alloys (α+γ2-aluminum bronzes) with high aluminum content are less ductile and are mainly used as foundry alloys.
It should be noted that the actual aluminum content in industrial alloys varies widely, which affects the stability of the mechanical properties of cast and deformed aluminum bronze semi-finished products.
Changes in the mechanical properties of aluminium bronzes processed by pressure (tensile strength σv, proportionality σnu and yield strength σ0,2, relative elongation δ and contraction ψ, impact toughness an (TC) and Brinell hardness (HB) depending on aluminum content, as shown in Fig.3.
Fig. 3: Variation of mechanical properties of Cu-Al bronzes depending on aluminum content:
a — strips deformed by 40% and annealed at 650oC for 30 min;
b — pressed bars and tubes of aluminum bronze БрАЖМц10−3-1,5
This feature of aluminum bronzes is considered in foreign national standards (USA, Germany, UK, France, etc.). These countries have a narrower interval of aluminum content in bronzes in order to improve stability of their mechanical properties which is about 1.5−2 times less than in similar bronzes used in CIS countries (see alloys GOST 493, GOST 17328 and foreign analogous alloys).
In the USA, France and Japan there are groups of bronzes of БрАЖМц type, in which the required mechanical properties are achieved only by changing the aluminum content.
Effect of alloying elements on the properties of aluminum bronzes
The alloying of two-part aluminum bronzes with different elements markedly changes their properties. The main alloying elements in Cu-Al alloys are iron, manganese and nickel. In aluminum bronzes, as a rule, the iron and nickel content does not exceed 5.5, manganese 3% (by mass).
Iron in the solid state is slightly soluble in Cu-Al alloys and forms with aluminum intermetallic compound of Fe3Al composition, which stands out as an independent phase in the form of finely dispersed particles. At a content of about 1% Fe in the alloys, a small number of fine particles is formed, located near the eutectoid region (α + γ2) and framing it. However, with increasing iron content their number increases. Thus, at a 4% Fe content, fine-dispersed particles Fe3Al are formed both in the region of α + γ2, and in the region of α. The finely dispersed particles of the intermetallic compound Fe3Al prevent grain growth in aluminum bronzes at high temperatures. Under the influence of iron, which greatly improves mechanical properties and delays the recrystallization temperature, the so-called phenomenon of «spontaneous annealing», which leads to increased brittleness of the alloys, disappears in aluminum bronzes. Iron, refining the structure, stops the formation in Cu-Al alloys containing 8.5−11.0% Al of coarse-grained γ2-phase, which stands out in the form of continuous chains, causing brittleness.
Iron, depending on its content in the alloy, affects the structure, phase transformations and properties of aluminum bronzes as follows: at up to 1.2% content, it is in solid solution (α-phase), and at higher content it is isolated in the form of individual globular inclusions, which in double and triple alloys containing nickel,.are usually represented by the k-phase. Approximate composition of the k-phase: 85% Cu, 10% Al and 5% Fe; at an alloy content of 1.2 to 5.5% iron has a strong modifying effect on the change of primary grain in castings; at an iron content > 5.5% Fe this effect disappears. Therefore, the iron content in industrial aluminum bronzes usually does not exceed 4%.
Iron hardens aluminum bronzes by increasing the strength of the solid solution (α-phase) and the separation of the k-phase. Alloys with high iron content such as BrAJ10−10 are highly resistant to abrasion and erosion, but less resistant in sea water.
Additional alloying of Cu-Al-Fe alloys with manganese and nickel considerably increases their strength characteristics and corrosion resistance, changes the structure and composition of the k-phase.
Manganese dissolves well in aluminum bronzes in the solid state. At Mn content > 2% in alloys of Cu-Al system, the transformation of α + γ2 phases into β phase significantly accelerates (manganese lowers the eutectoid temperature and delays the decay of β-phase); at Mn>8% the decay of β-phase practically does not occur.
A feature of manganese additives in aluminum bronzes is also the appearance in them during cooling of needle nuclei of β-phase before the conversion of β-phase to α+ γ2
The appearance of α-phase needle nuclei is especially noticeable during annealing of large semi-finished products. Therefore, special aluminum-manganese bronzes with high manganese content are widely used for casting marine propellers with different thicknesses from 15 to 400 mm.
Manganese is the leading element in bronzes of БрАЖ10−4, БрАЖ9−4 types, which determines kinetics of β-phase transformation upon heating and improves their hardenability on depth. The content of Mn in these bronzes is allowed up to 1.5%. But with increasing Mn content from 2 to 5% the hardness of aluminum bronzes after quenching at 800−1000°C decreases. Therefore, to increase the hardness of aluminum bronzes during heat treatment, they should contain no more than 0.5% Mn.
Manganese increases mechanical and corrosion properties and improves technological characteristics of Cu-Al alloys. Aluminum bronzes alloyed with manganese are characterized by increased corrosion resistance, cold resistance and high deformability in hot and cold state.
Nickel, which is insoluble in solid state in copper, is almost insoluble in aluminum (at 560 °C solubility is 0.02%). Nickel increases the α-phase region in Cu-Al and Cu-Al-Fe systems. In Cu-Al-Ni alloys under the influence of nickel the solid solution area shifts considerably towards the copper angle with decreasing temperature, so they can be subjected to dispersion hardening. The dispersion hardening ability of these alloys is found at 1% Ni content. Nickel increases the eutectoid decomposition temperature of β to α+γ2 to 615 °C and delays the transformation of α+γ2 into β upon heating. The effect of nickel becomes especially noticeable at its content of more than 1.5%. Thus, with 2% Ni in the alloy the β-phase appears at 790 °C, with 4% Ni — at 830 °C.
Nickel has a favorable effect on the structure of eutectoid α+γ2 and pseudoeutectoid α + β, significantly increases the resistance of phase transformations of β-phase, and during casting and hardening promotes a greater amount of metastable β'-phase of martensitic type. In this case the α-phase becomes more rounded, the structure becomes more uniform, the dispersity of eutectoid increases.
Nickel alloying of aluminum bronzes significantly increases their physical and mechanical properties (thermal conductivity, hardness, fatigue strength), cold resistance and antifriction characteristics, corrosion and erosion resistance in seawater and weak hydrochloric acid solutions; heat resistance and recrystallization temperature without noticeable deterioration of technological characteristics. The nickel content in the alloys significantly increases the modifying effect of iron.
Aluminum bronzes of Cu-Al-Ni system are rarely used. Nickel is usually introduced into aluminum bronzes in combination with other elements (mostly iron). Aluminum bronzes of БрАЖН10−4-4 type are most widely used. Optimal properties of these bronzes are achieved at Fe: Ni ratio = 1:1. In these bronzes with 3% Ni and 2% Fe k-phase can be allocated in two forms: in the form of small round inclusions of solid solution on the basis of iron, alloyed with aluminum and nickel, and in the form of thin plates, intermetallide of NiAl composition.
The most widely used deformed aluminum bronzes of the following systems: Cu-Al, Cu-Al-Fe, Cu-Al-Mn, Cu-Al-Fe-Mn, Cu-Al-Fe-Ni.
Aluminum bronzes are highly corrosion resistant in carbon dioxide solutions, as well as in solutions of the majority of organic acids (acetic, citric, lactic and others), but they are unstable in concentrated mineral acids. In solutions of sulfuric acid salts and caustic alkalis single-phase aluminum bronzes with reduced aluminum content are more stable.
Aluminum bronzes are less susceptible to corrosion fatigue than other materials.
Peculiarities of machining deformable aluminum bronzes
In order to obtain homogeneous deformed semi-finished products with improved mechanical properties and high fatigue strength, it is recommended that aluminum bronzes be cast by continuous method, and the subsequent processing be carried out by a special method that includes operations:
a) hot machining of the cast billet with total compression up to 30%;
b) heat treatment at a given temperature (t0) with a deviation of ± 2 ° C (heating to a given temperature, delay 20 min at every 25 mm of the cross-section of the material);
c) hardening in water or oil at 600 °C;
d) hot work by pressure at a temperature 35−50 ° C less than that adopted in the heat treatment stage «b» depending on the aluminum content in the alloy (aluminum content must be defined with an accuracy of ±0,02%). The heat treatment temperature is determined by the empirical formula:
t=(1990 — 1000A)°C,
where, A — the aluminum content in the alloy, % (by mass).
The graphical dependence of temperature on aluminum content during heat and second hot workings with pressure on aluminum bronzes is shown in Fig. 4.
Fig. 4. Dependence of temperature on aluminum content during heat and hot workings with pressure on aluminum bronzes:
1 — temperature of heat treatment;
1 — temperature of thermal treatment; 2 — temperature of hot work with pressure
Beryllium bronzes (copper-beryllium alloys)
Beryllium bronzes are unique alloys by their favorable combination of good mechanical, physical and chemical and anticorrosive properties. These alloys after quenching and deoxidizing have high tensile strength, elasticity, fluidity and fatigue life, are highly conductive, heat conductive, hard, have high creep resistance, high cyclic strength with minimum hysteresis, high corrosion and corrosion fatigue resistance. They are frost-resistant, non-magnetic and do not produce sparks on impact. Therefore beryllium bronzes are used for production of springs and springing parts for critical applications, including membranes and clockwork parts.
Fig. 5. State diagram of the Cu-Be system
The diagram shows that copper and beryllium form a series of solid solutions. The solid solution region α at 864 °C reaches 2.7% (by mass). With decreasing temperature, the solubility boundary of the α region shifts quite sharply toward copper. At the eutectoid transformation temperature of 608 °C it is 1.55% and decreases to 0.2% at 300 °C, indicating that beryllium bronzes can be enriched.
Significant change of beryllium concentration in α-solid solution with decreasing temperature promotes dispersion hardening of Cu-Be alloys. The effect of dispersion hardening of Cu-Be alloys on the beryllium content is shown in Figure 6.
Figure 6. Influence of beryllium content on the dispersion hardening effect of Cu-Be alloys: 1 — quenching at 780 °C; 2 — quenching at 780 °C + tempering at 300°C
Thermal treatment of beryllium bronzes is carried out at 750−790 ° C followed by quenching in water to obtain a supersaturated solid solution. In this state beryllium bronzes easily tolerate operations of bending, drawing and other types of deformation. The second operation of heat treatment — tempering is carried out at a temperature of 300−325 ° C. The β'-phase is released. These allocations are associated with significant lattice stresses, which cause an increase in hardness and strength of the alloys.
The eutectoid transformation of the β-phase at temperatures below 608 °C results in the formation of α + β' eutectoid. Phase α has a cubic face-centered lattice, the parameter of which decreases with increasing beryllium content. The β phase has a cubic volumetric centered lattice with a disordered arrangement of atoms. The crystal structure of the β'-phase is the same as that of the β-phase, but it has an ordered arrangement of beryllium atoms.
In practice, binary copper-beryllium alloys are almost never used, three- and multicomponent alloys are widespread.
Nickel, cobalt and iron are added to Cu-Be alloys to slow down phase transformations and recrystallization with obtaining a more homogeneous structure. The total content of nickel, cobalt and iron in beryllium bronzes ranges from 0.20 to 0.60% (by mass), including nickel and cobalt from 0.15 to 0.35% (by mass).
The introduction of titanium into Cu-Be alloys, which forms a strengthening phase with beryllium, helps to slow down the diffusion processes in them. Titanium, as the surface active element, reduces the concentration of beryllium at the grain boundaries and reduces the diffusion rate in these areas. In beryllium bronze with titanium additives a homogeneous decomposition and, as a consequence, a more uniform hardening is observed.
Titanium has the most favorable effect on the properties of beryllium bronze in the presence of nickel. Due to the addition of titanium and nickel, the beryllium content in the alloys can be reduced to 1.7−1.9% (by mass).
Manganese in Cu-Be alloys can partially replace beryllium without a noticeable reduction in strength. Alloys Cu + 1% Be + 5−6% Mn and Cu + 0.5% Be + 10% Mn after dispersion curing approach to the mechanical properties of beryllium bronze BrB2 grade.
Magnesium additives in small amounts (0.1%) increase the effect of dispersion hardening of beryllium bronze, and in the range from 0.1 to 0.25% noticeably reduce its plasticity.
Lead, bismuth and antimony for beryllium bronzes are very harmful impurities that worsen their deformability in the hot state.
In standard Cu-Be alloys, the content of Al and Si is not allowed to exceed 0.15% of each element. In such concentrations, these elements do not adversely affect the properties of the alloys.
Manganese bronzes
Manganese bronzes are characterized by high mechanical properties. These alloys are perfectly workable by pressure both in hot and cold condition, allowing deformation during cold rolling up to 80%.
Manganese bronzes are characterized by corrosion resistance, increased heat resistance and are therefore used for the manufacture of parts and products operating at elevated temperatures. In the presence of manganese the recrystallization temperature of copper increases by 150−200°C.
Fig. 7. Diagram of state of the Cu-Mn system.
Manganese at elevated temperatures is unrestrictedly soluble in copper both in the liquid and in the solid state. When the alloy contains 36.5% magnesium (by mass) the liquidus and solidus temperature of the system is the same and amounts to 870 ± 5 °C. With decreasing temperature a number of transformations occur and new phases are distinguished. The solid solution area y decreases with decreasing temperature. Manganese bronzes containing less than 20% magnesium are single-phase in the temperature range from room temperature to the melting point. Fig. 8 shows the dependence of mechanical properties of manganese bronzes on the manganese content.
Fig. 8. Changes in mechanical properties of Cu-Mn alloys depending on manganese content: а — yield strength σ0,2; b — tensile strength σb; c — relative elongation δ
The most widely used bronze BrMc5, which deforms well in hot and cold conditions, has high corrosion resistance and retains its properties at elevated temperatures.
Silicon bronzes
Silicon bronzes are characterized by high mechanical, springiness and antifriction properties, are resistant to corrosion and wear resistance. These alloys are perfectly workable by pressure in both hot and cold state, well welded with steel, solderable by both soft and hard solders. They are non-magnetic, do not give sparks on impact and do not lose ductility at very low temperatures.
State diagram of the Cu-Si alloy system:
Figure 9. State diagram of the Cu-Si system
As can be seen from the diagram, the solid solution boundary α reaches 5.4% Si (by mass) at 830oC and shifts towards copper with decreasing temperature. Phase α has a cubic face-centered lattice with parameter a=(3.6077+0.00065k) Å, where k is the silicon concentration, %.
At temperature > 577 oC to the right of the α-solid solution boundary a new co-phase with a hexagonal densely packed lattice (a=2.5550 Å, c=4.63644 Å) appears. A distinctive feature of the phase k is a noticeable change in coloring in polarized light from light to dark brown. At 557o C the phase transformation k → α+ γ occurs.
The character of silicon change in α-solid solution with decreasing temperature testifies to the possibility of ennoblement of some alloys of Cu-Si system. However, the effect of dispersion hardening of alloys is weak and is not used in practice.
Silicon bronzes with the addition of manganese and nickel are the most common. Two-component bronzes with additions of tin, zinc, iron and aluminum are used less frequently.
The alloying of copper-silicon bronzes with manganese can significantly improve their mechanical properties and corrosion resistance.
Diagram of state of Cu-Si-Mn system:
Figure 10. State diagram of the Cu-Si-Mn system. Saturation isotherm of the solid solution region
In spite of the shift of the boundary of the α-region with decreasing temperature towards the copper corner, the ennoblement effect of Cu-Si-Mn alloys is weakly pronounced.
Nickel additives markedly increase the mechanical properties of silicon bronzes. Silicon and nickel form an intermetallic compound (Ni2Si), which visibly dissolves in copper. As the temperature decreases (from 900 to 500o C) the solubility of Ni2Si in copper decreases sharply and the dispersed particles of intermetallic compound that are released during this process harden the alloys. Heat treatment (quenching, aging) increases the strength and hardness of these alloys by almost 3 times compared to annealed alloys. After quenching Cu-Si-Ni alloys have high ductility and excellent cold workability.
Variation of the tensile strength of these alloys depending on the Ni2Si content and the method of heat treatment:
Figure 11. Changes in strength of Cu-Ni-Si alloys depending on Ni2Si content and heat treatment: 1 — quenching at 900−950°C; aging at 350−550°C; 2 — annealing at 800 °C; 3 — quenching at 900−950°C
Cobalt and chromium additives have the same effect on silicon bronzes as nickel, but the effect of dispersion hardening of alloys under the influence of cobalt and chromium silicides is much weaker.
Additions of small amounts of Sn (up to 0.5%) noticeably increase and iron reduces the corrosion resistance of silicon bronzes. For this reason, in silicon bronzes processed by pressure, Fe content should not exceed 0.2−0.3% (by mass).
The addition of Zn within the range of 0.5% to 1.0% in the melting of silicon bronzes contributes to improving their technological properties.
The alloying of silicon bronzes with aluminum increases their strength and hardness, but the alloys of Cu-Si-Al system are not widespread because of their poor welding and brazing.
Arsenic, phosphorus, antimony, sulfur and lead are harmful impurities in pressure-treated silicon bronzes.
Corrosion properties of silicon bronzes
Silicon bronzes have excellent corrosion resistance under the influence of sea, industrial and rural atmospheres, fresh and sea water (at a flow rate of 1.5 m/s), hot and cold concentrated alkali and sulfuric acid solutions and cold solutions of hydrochloric and organic acids, chlorides and sulfates of light metals. They are quite stable in the atmosphere of dry gases: chlorine, bromine, fluorine, hydrogen sulfide, hydrogen fluoride and chloride, sulfuric gas and ammonia, but they corrode in these environments in the presence of moisture.
However, silicon bronzes are poorly resistant against the effects of aluminum hydroxide, chlorides and sulfates of heavy metals. They quickly corrode in acidic mine water containing Fe2 (S04)3, as well as in solutions of salts of chromic acids.
Peculiarities of heat treatment of siliceous bronzes
Light annealing of silicon bronzes (including heating and cooling) should be performed in water vapor. Oxide films formed on the surface of semi-finished products in the course of annealing are easily removed by pickling at room temperature in 5% sulfuric acid solution.
Tin bronzes
Tin bronzes are alloys of various compositions based on Cu-Sn system. The summary list of Russian tin bronzes processed by pressure and their foreign analogous alloys is given in Table 4.
Summary list of domestic pressure-treated tin bronzes and their foreign analogues
Tin phosphor bronzes:
Make of domestic bronze | US analogue | Analog German | Analog Japan |
---|---|---|---|
BrOF2−0,25 | - | - | - |
BrOF4−0,25 | С51100 | CuSn4 (2.1016) | C5111 |
- | C53400 | - | - |
BrOF6,5−0,15 | - | CuSn6 (2.1020) | C5191 |
- | C51000 | - | - |
- | C53200 | - | - |
BrOF6,5−0,4 | - | - | - |
BrOF7−0,2 | - | SuSn6 (2.1020) | C5210 |
BrOF7−0,2 | - | SuSn8 (2.1030) | - |
BrOF8.0−0.3 | C52100 | Same | C5212 |
- | C52400 | - | - |
Tin-zinc bronzes:
Domestic Bronze Brand | US analogue | Same as Germany | Japan analogue |
---|---|---|---|
BrOC4−3 | - | - | - |
- | - | CuSn6Zn6 (2.1080) | - |
Tin-nickel bronzes:
Domestic Bronze Brand | US analogue | Analog Germany | Analog Japan |
---|---|---|---|
- | C72500 | CuNi9Sn2 (2.0875) | - |
- | C72650 | - | - |
- | C72700 | - | - |
- | C72900 | - | - |
Tin-zinc-lead bronzes:
Domestic Bronze Brand | US analogue | Same as Germany | Japan analogue |
---|---|---|---|
BrOZS4−4-2,5 | - | - | - |
- | С54400 | - | - |
BrOtzS4−4-4 | - | - | - |
The Cu-Sn system state diagram is shown in Fig. 12.
Fig. 12 Diagram of state of system Cu-Sn
The α-solid solution of tin in copper (face-centered cubic crystal lattice) is malleable in hot and cold states.
Phases β and γ are stable only at elevated temperatures, and decay at a high rate with decreasing temperature. Phase δ (Cu31Sn8, lattice γ-phase) is the product of γ-phase (or β') decay at 520 °C, hard and brittle.
Decomposition of δ-phase into α + Cu3Sn (ε-phase) starts at 350 °C. With decreasing temperature the decomposition of δ-phase proceeds extremely slowly (during long annealing after cold deformation by 70−80%). Practically in alloys containing up to 20% Sn the ε-phase is absent.
In technical tin bronzes the tin content varies from 2% to 14%, less frequently up to 20%.
Alloys of the Cu-Sn system, depending on the content of tin, consist of either homogeneous crystals of α-solid solution, or crystals of α and eutectoid α + β.
The diffusion process in tin bronzes proceeds slowly The dendritic structure disappears only after multiple cycles of thermomechanical processing. For this reason it is difficult to pressure treat tin bronzes.
During melting tin bronzes are deoxidized with phosphorus, therefore most of Cu-Sn binary alloys contain residual phosphorus. Phosphorus is considered an alloying additive when its content in the alloy is > 0.1%.
The main alloying additives in tin bronzes, in addition to phosphorus, are lead, zinc and nickel.
Effect of alloying additives
Phosphorus interacting with copper gives the compound Cupr (14.1% P), which at a temperature of 714 ° C forms with copper eutectics (P content — 8.4% (by mass). In the ternary system Cu-Sn-P, a ternary eutectic is formed at 628 °C, containing, %:80.7Cu, 14.8 Sn and 4.5P.
From the state diagram of the Cu-Sn-P system (Fig. 13) it can be seen that with increasing tin content and decreasing temperature the saturation boundary of the α-solid solution shifts sharply towards the copper angle.
Fig. 13. State diagram of the Cu-Sn-P system: a — copper angle; b — polymetric sections of copper angle of the Cu-Sn-P system at a constant tin content
At the content > 0.3% P in tin bronzes the last stands out as inclusions of phosphide eutectics. Tin bronzes with 0.5% P and higher easily deteriorate during hot deformation because the phosphide eutectic melts. Therefore, the maximum phosphorus content of pressure-treated tin bronzes is 0.4%. With this phosphorus content tin bronzes have optimal mechanical properties, have increased modulus of normal elasticity, elasticity and fatigue limits. Using an annealing-homogenization, after which a significant portion of phosphorus passes into α-solid solution, it is possible to improve the deformability of tin bronzes with high phosphorus content.
Small additions of zirconium, titanium, boron and niobium also improve the hot and cold workability of tin bronzes.
Lead is virtually insoluble in tin bronzes in the solid state. During solidification of the alloy it is released as an independent phase in the form of dark inclusions between dendrites. Lead markedly improves density, antifrictionality and machinability of tin bronzes, but significantly reduces their mechanical properties. Antifriction tin bronzes contain up to 30% Pb.
Zinc is well soluble in tin bronzes in solid state and, changing insignificantly the structure of alloys, significantly improves their technological properties.
Nickel shifts the solid solution boundary α towards the copper angle (Fig.14).
Fig. 14. State diagram of the Cu-Sn-Ni system: а — section of the copper angle at the nickel content of 2%; b — region of the solid solution saturation limit at room temperature. Copper angle.
The crystal lattice of α-solid solution under the influence of nickel does not change, but its parameter increases slightly (-0.007 A). At low concentrations of tin, a new phase (Ni4Sn) appears in the heterogeneous region, which, depending on the rate of solidification, stands out either as small needle-like crystals (rapid cooling) or light blue inclusions. The liquids in Cu-Sn alloys increase markedly when alloyed with nickel. At 539 °C the eutectoid transformation of α + γ into α + β' occurs. The δ' phase is polarized unlike the δ phase of the Cu-Sn double system.
Nickel increases mechanical properties and corrosion resistance of tin bronzes, refines their structure and at 1% content is a useful additive. At >1% Ni, although alloys are ennobled, their machinability to pressure deteriorates. Nickel has a particularly drastic effect on tin-phosphor bronzes. At the same time, Ni at the content within 0.5−1% does not affect either the structure or the properties of tin-zinc bronzes.
The influence of impurities
Aluminum, magnesium and silicon impurities are very detrimental in tin bronzes. Though these elements included in solid solution improve mechanical properties of bronzes, but they oxidize during melting and form refractory oxides, which are located along the grain boundaries and break the bond between them.
The impurities of arsenic, bismuth, antimony, sulfur and oxygen are also detrimental to tin bronzes processed by pressure. The latter reduces the anti-friction characteristics of tin bronzes.
Corrosion properties
Tin bronzes are highly resistant to atmospheres (rural, industrial and sea water). They are more resistant in seawater than copper and brass (resistance of bronzes to seawater increases with increasing tin content). Nickel also increases the corrosion resistance of tin bronzes in seawater, while lead at high content decreases it. Tin bronzes are stable in salt water.
Tin bronzes are satisfactorily resistant to corrosion in an atmosphere of superheated steam at 250 °C and a pressure notTin bronzes are also fairly resistant to corrosion in an atmosphere of superheated steam at 250 °C at a pressure no higher than 2.0 MPa, under the influence of room temperature solutions of alkali, dry gases (chlorine, bromine, fluorine and their hydrogen compounds, carbon and sulfur oxides, oxygen), carbon heterochloride and ethylene chloride.
Tin bronzes are unstable in the environment of mineral (nitric, sulfuric) and fatty acids, alkali, ammonia, cyanide, iron and sulfur compounds, gases (chlorine, bromine, fluorine) at high temperature and acidic mine water.
The corrosion of tin bronzes under the action of sulphuric acid increases in the presence of oxidizers (K2Cu7, Fe2 (S04)3, etc.) and decreases 10−15 times in the presence of 0.05% benzylthiocyanate.
The corrosion rate of tin bronzes under the action of a number of agents is as follows, mm/year:
Alkalis:
hot …1,52
at temperature of 293 K …0,4−0,8
ammonia solutions at room temperature …1.27−2.54
acetic acid at room temperature …0.025−0.6
H2S vapor at 100 °C …1.3
wet sulfur dioxide …2.5
dry and wet water vapor (depending on the flow rate) …0.0025−0.9
Tin bronzes are susceptible to stress corrosion cracking when exposed to mercuric nitrate.
Brass, iron, zinc and aluminum are protectors for tin bronzes during electrochemical corrosion.